Powder doser
Powder doser
For safe dosing of chemicals in your lab. Unique powder pump for free-flowing solid substances.
The LAMBDA DOSER & Hi-DOSER powder feeder is a unique programmable powder pump for free-flowing solid substances.
It allows automated continuous dispensing or intermittent addition (with pauses) of powders, powdery and crystalline substances without a spoon.
The powder dispensers with an optional foot-switch can be used to dispense the powder in portions in media preparation, monitoring and screening.
LAMBDA DOSER / Hi-DOSER powder feeder will modernize your laboratory
The powder dispenser consists of a dosing unit coupled to a digitally controlled stepping motor, allowing the constant and reproducible dosing of solids. As the DOSER / Hi-DOSER powder feeder offers different control options, it can also be used in automatically controlled processes. Automation of the powder dispensing process in the life sciences, pharmaceutical or analytical laboratory can be done with the programmable powder dosing pump as it reduces human error, risk of spillage and conforms to laboratory safety standards.Powder dispenser image gallery
The powder dosing instruments such as DOSER 0.2 L, DOSER 1 L, DOSER 3 L, Hi-DOSER 1 L, Hi-DOSER 3 L and its accessories & consumables can be viewed at www.lambda-instruments.com/powder-doser/doser-hidoser-image-gallery/. Types of LAMBDA DOSER and Hi-DOSER powder feeding equipment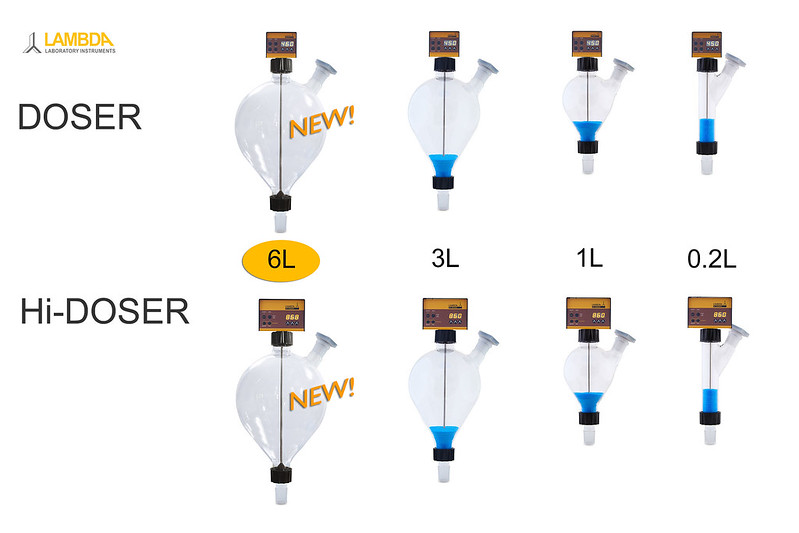
Properties of LAMBDA DOSER / Hi-DOSER powder dosing instrument
Dosing rate of powder dispenser
The dosing speed can be set directly on the control display of the powder feeder or remotely from 0–999 speed range for precise and reproducible solid flow rate. The powder dosing rate depends mainly on the powder properties. For example, the dosing rate range of NaCl at our laboratory conditions:- LAMBDA DOSER: 50 mg/min to 50 g/min
- LAMBDA Hi-DOSER, slow mode*: 60 mg/min to 60 g/min
- LAMBDA Hi-DOSER, fast mode*: 250 mg/min to 250 g/min
Program dosing speed, time and pauses
Dosing speeds and dosing times with pauses can be easily programmed locally on the pump display. The entered program can be repeated 'n' number of times (1-99 or infinite loop) with the “cycle” setting in the program.Volume of storage vessels
DOSER and Hi-DOSER powder feeders are supplied with the following glass vessels:- Approx. 200 ml or 0.2 L glass vessel
Corresponds to 250 g NaCl, 200 g NaHCO3 or 150 g sucrose. This capacity is optimal for most laboratory applications. - 1 L glass vessel (approx. 1 L volume)
- 3 L glass vessel (approx. 3 L volume)
Remote control of powder pump
The whole speed range of powder dispensing can be remotely controlled by applying a voltage of 0-10V. Switching the powder feeder on and off (ON/OFF) is controlled by an external contact or 12V signal. The RS-485 or RS-232 interface (optional) allows for enhanced PC control (variable flow rates, flow profile, etc.). A PC control software PNet is also available (optional). Please refer the LAMBDA DOSER / Hi-DOSER User Manual for connection details.Data storage and visualization
The PNet PC control software is ideal for remote control of dosing units, data storage and visualization of powder dosing. You can connect up to 6 powder dispensers via RS-485 interface and cables to USB or serial port of the computer, without having to purchase additional software licenses for the additional laboratory equipment. The PNet software allows to create dosing profile, record data for analysis or comparison, visualize real time trends and to save data to PC.Conformity to safety in lab
The powder dispensers LAMBDA DOSER and LAMBDA Hi-DOSER allows a safe and reproducible dosing of hazardous chemicals in the lab and conforms to modern safety rules. To protect the laboratory technician or researcher or student, the powder dosing device can also be controlled remotely. The hermetic construction of the DOSER and Hi-DOSER allows safe handling of dangerous and toxic solid substances. Several seals make the DOSER air-tight and it can be used with a slight over- or under-pressure. If the powder sample has to be protected from agglomeration or reaction with air humidity, the glass vessel can be purged with inert gas or dry air using the supplied gassing plug. If the process needs to be protected from the risk of breakage, you can also order the glass vessels with a silicone coating (outside). All parts in contact with the powdery substances are made of chemically resistant materials.Quality standards for powder dosing
LAMBDA DOSER / Hi-DOSER powder feeders are recommended for high quality standard of powder dosing in the laboratory. In addition to the digital setting and precise dosing mechanism, the automatic recording of dosing data makes it an optimal choice to dispense powders under GMP and GLP.Simple and easy to use lab device
The lab powder dispensers DOSER and Hi-DOSER has been designed specially for easy assembly and cleaning.Fixing to lab equipment: By standard glass adapters
The DOSER and Hi-DOSER can be coupled to all common glass recipients having standard ground fittings NS 29/32 or SVL threaded connectors. It can also be fitted to the reactor vessel using an adaptor. Special attention has been paid to minimizing the dimensions of all parts of the powder dispenser. Thus, DOSER 0.2 L can be adapted easily to complex laboratory installations. The robust construction and the use of high quality materials assure a long lifetime of the powder feeders.Economic dispensing of powder portions
Automated dispensing of powder portions in the lab gives the time for the lab staff to work on other tasks. Due to better reproducibility and elimination of errors, the number of experiments can be reduced. The DOSER and Hi-DOSER offers an excellent price-performance ratio.Quantification of the dosed substances
The powder DOSER can be configured with the electronic LAMBDA INTEGRATOR (optional) and allows the quantification of the amount of powder added as a function of time. This provides important information on the processes or reactions, e.g. when the DOSER is controlled by a controller (pH-stat, thermostat, etc.).
Type: LAMBDA DOSER / HI-DOSER – microprocessor-controlled programmable powder dosing instrument
Programming: DOSER: up to 27 steps of speed and time; HI-DOSER: up to 99 steps of speed and time
Time resolution: 0 to 999 minutes in 1 minute steps or 0 to 99.9 minutes in 0.1 minute steps: time resolution can be selected individually for each program step
Motor: DOSER: microprocessor controlled stepping motor; HI-DOSER: microprocessor controlled brushless long life BLDC motor with neodymium magnets
Speed control range: 0 to 999
Interface: RS-485 (optional) or RS-232 (optional)
Power supply: DOSER: 95–240 V/50–60 Hz AC plug-in power supply with DC 12V/12W output; HI-DOSER: 95–240 V/50–60 Hz AC plug-in power supply with DC 12V/50W output; possible field operation on 12 V accumulator
Volume: Approx. 0.2 L, 1 L and 3 L glass vessels
Dimensions: DOSER motor unit: 6 (H) x 7 (W) x 13 (D) cm; HI-DOSER motor unit: 10.5 (W) x 9.5 (H) x 13 (D) cm; Glass vessel approx. 0.2 L: 30 (H) x12 (W) x 5 (D) cm; Glass vessel approx. 1 L: 30 (H) x 18 (W) x 14 (D) cm; Glass vessel approx. 3 L: 38 (H) x 21 (W) x 17.5 (D) cm
Safety: CE, meets IEC 1010/1 norm for laboratory instruments
Operation temperature: 0 - 40 °C
Operation humidity: 0-90% RH, not condensing
Remote control: 0–10 V DC (dosing speed control), 3–12 V DC (ON/OFF control); (option 0-20 or 4-20 mA)
Software: PC control software PNet (optional)
Programming: DOSER: up to 27 steps of speed and time; HI-DOSER: up to 99 steps of speed and time
Time resolution: 0 to 999 minutes in 1 minute steps or 0 to 99.9 minutes in 0.1 minute steps: time resolution can be selected individually for each program step
Motor: DOSER: microprocessor controlled stepping motor; HI-DOSER: microprocessor controlled brushless long life BLDC motor with neodymium magnets
Speed control range: 0 to 999
Interface: RS-485 (optional) or RS-232 (optional)
Power supply: DOSER: 95–240 V/50–60 Hz AC plug-in power supply with DC 12V/12W output; HI-DOSER: 95–240 V/50–60 Hz AC plug-in power supply with DC 12V/50W output; possible field operation on 12 V accumulator
Volume: Approx. 0.2 L, 1 L and 3 L glass vessels
Dimensions: DOSER motor unit: 6 (H) x 7 (W) x 13 (D) cm; HI-DOSER motor unit: 10.5 (W) x 9.5 (H) x 13 (D) cm; Glass vessel approx. 0.2 L: 30 (H) x12 (W) x 5 (D) cm; Glass vessel approx. 1 L: 30 (H) x 18 (W) x 14 (D) cm; Glass vessel approx. 3 L: 38 (H) x 21 (W) x 17.5 (D) cm
Safety: CE, meets IEC 1010/1 norm for laboratory instruments
Operation temperature: 0 - 40 °C
Operation humidity: 0-90% RH, not condensing
Remote control: 0–10 V DC (dosing speed control), 3–12 V DC (ON/OFF control); (option 0-20 or 4-20 mA)
Software: PC control software PNet (optional)
- DE - Pulverdosiergerät LAMBDA DOSER und HI-DOSER - Prospekt (pdf)
- DE - Bedienungsanleitung - LAMBDA DOSER Pulverdosiergerät (pdf)
- ES - Dosificador de solidos LAMBDA DOSER / HI-DOSER (pdf)
- ES - Instrucciones de uso - Dosificadora de sólidos y sustancias pulverulentas LAMBDA DOSER (pdf)
- RU - Дозаторы порошков LAMBDA DOSER и HI-DOSER - Листовка (pdf)
- RU - Руководство по эксплуатации - Дозаторы порошка LAMBDA DOSER и HI-DOSER (pdf)
- FR - Mode d'emploi - LAMBDA DOSER doseur de poudres programmable (pdf)
- FR - LAMBDA DOSER / HI-DOSER doseur de poudres programmable - brochure (pdf)
- CZ - Návod k obsluze - Dávkovač pevných, krystalických látek a prášků LAMBDA DOSER (pdf)
- CZ - Automatický dávkovač pevných, krystalických látek a prášků LAMBDA DOSER (pdf)
- EN - LAMBDA DOSER and HI-DOSER powder dosing instrument - Leaflet (pdf)
- EN - Operation manual - LAMBDA DOSER and HI-DOSER powder dosing instrument (pdf)
- EN - Application note - LAMBDA powder DOSER - Reproducible powder dosing (pdf)
2024
The heat treated wet-silica solid was loaded in the LAMBDA solid DOSER and added to the reactor. Luo, L., Rix, F. C., Stevens, K. A., Kuo, C. L., Zhang, X., Lovell, J. A., Harlan, C.J., Ye, X., & Berg, B. R. (2024). Improved In-Situ MAO Derived Silica Supported Single-Site Metallocene Catalysts. U.S. Patent Application No. 18/253,867.
https://patents.google.com/patent/US20240092947A1/en (2024 June 17)
For “flash pyrolysis” experiments, the powdered biomass (mixture of cellulose, hemicellulose, lignin and ash) was fed into the nitrogen line inside a venturi using a „dust feeder“ LAMBDA Hi-DOSER at a rate between 1 and 20 g/mn. Proust, C., Proust, M., & Foyer, J. (2024, February). High temperature pyrolysis of lignocellulosic biomass for biogas production. In Technological Systems, Sustainability and Safety.
https://hal.science/hal-04538203 (2024 May 14)
Solids segregation studies: The solids dispenser on the top of the fluidized bed reactor was a LAMBDA DOSER 3L that added continuous solid at a speed of up to 13.7 g/min. Ciércoles, R., Lasobras, J., Soler, J., Herguido, J., & Menéndez, M. (2024). A Preliminary Assessment of Sorption Enhanced Methanol Synthesis in a Fluidized Bed Reactor with Selective Addition/Removal of the Sorbent. Removal of the Sorbent.
https://dx.doi.org/10.2139/ssrn.4735903
Before starting pyrolysis, 6 g materials were mixed evenly and added to the feeder LAMBDA DOSER 0.2L Wang, X., Peng, Y., Zhou, R., Fan, L., Zhang, Q., Cui, X., Wu, Q., Zeng, W., Tian, X., Ke, L., Ruan, R., & Wang, Y. (2024). Production of monocyclic aromatic hydrocarbons from microwave co-pyrolysis of polyethylene terephthalate and low-density polyethylene using coconut husk carbon as microwave absorbent. Chemical Engineering Journal, 150732.
https://doi.org/10.1016/j.cej.2024.150732
Study about the significance of feedstock characteristics (moisture, volatile matter, fixed carbon and ash contents) during the particle feeding stage for downdraft gasification of biomass waste: Lambda powder dosing equipment (LAMBDA DOSER 0.2L) was used for particle feeding (date palm waste, olive pomace, sewage sludge) and gasifier flow rate, power rating & storage time were tested. Khan, S., Adeyemi, I., Moustakas, K., & Janajreh, I. (2024). Investigating the characteristics of biomass wastes via particle feeder in downdraft gasifier. Environmental Research, 118597.
https://doi.org/10.1016/j.envres.2024.118597
2023
The automatic dosing equipment LAMBDA DOSER was used to feed continuously 70 % – 80 % of Al2O3 required for theoretical 100 % current efficiency. The system limites due to critical clogging in the alumina feeding channel were reached in some cases after 6 to 10 h. Singh, K., Gunnarsson, G., Magnusson, J. H., Haarberg, G. M., & Saevarsdottir, G. (2023). Performance Evaluation of Low-Temperature KF-NaF-AlF3 Electrolytes for Aluminum Electrolysis Using Vertical Inert Cu–Ni–Fe Alloy Anodes. Journal of The Electrochemical Society, 170(11), 113507.
https://doi.org/10.1149/1945-7111/ad0bae
Lithium-Ion Battery: Feeding of precursor powder (Silicon & ferrocene [Fe(C5H5)2]; 1 g/min) into surface-wave-sustained (SWS) plasma column (core temperature >4000 K) Jie, Z., Zhang, Z., Bai, X., Ma, W., Zhao, X., Chen, Q. & Zhang, G. (2023). Surface-wave-sustained plasma synthesis of graphene@Fe–Si nanoparticles for lithium-ion battery anodes. Appl. Phys. Lett. 11 September 2023; 123 (11): 113902.
https://doi.org/10.1063/5.0159269
2022
The sample of HDPE granules was placed in the glass granule doser (LAMBDA DOSER 1L) Dai, L., Zhou, N., Lv, Y., Cobb, K., Chen, P., Wang, Y., Liu, Y., Zou, R., Lei, H., Mohamed, B. A., Ruan, R., & Cheng, Y. (2022). Catalytic reforming of polyethylene pyrolysis vapors to naphtha range hydrocarbons with low aromatic content over a high silica ZSM-5 zeolite. Science of The Total Environment, 847, 157658.
https://doi.org/10.1016/j.scitotenv.2022.157658
Experimental channel for magnetic particles separation: In the first step, the fly ash was dosed by a LAMBDA dosing system with 1L vessel (mounted above a tray in the middle of the cross-section of the channel) into the horizontal channel and got dispersed by compressed air (3 bar) flowing from a flat nozzle onto the tray. Czech, T. (2022). Morphology and chemical composition of magnetic particles separated from coal fly ash. Materials, 15(2), 528.
https://doi.org/10.3390/ma15020528
Powder dosing of Al2O3 and other dried sieved particles in a closed-loop aerosol generator: The particles were dosed with a volumetric powder doser LAMBDA DOSER 0.2 L into a 1⁄4” T-piece where the powder got picked up by a stream of compressed air (5 L/min) and guided as aerosol through the installation stream. Prüfert, C., Beitz, T., Reich, O. & Löhmannsröben, H.-G. (2022). Inline process analysis of copper-bearing aerosols using laser-induced breakdown spectroscopy, laser-induced incandescence and optical imaging. Spectrochimica Acta Part B: Atomic Spectroscopy 197 (2022) 106527.
https://doi.org/10.1016/j.sab.2022.106527
Coal particles were introduced into the reactor through a N2-purged microprocessor-controlled programmable powder pump feeder (Hi-DOSER, LAMBDA) positioned above the reactor tube...The advantage of this powder pump feeder is that the feeding amount is relatively uniform, avoiding the clogging of the feeder and instability of the gas production. Dai, T., Xu, C., Zhang, Q., Liu, X., Chang, Z. & Yang, Y. (2022). Experimental study of the solar-driven steam gasification of coal in an improved updraft combined drop-tube and fixed-bed reactor. Energy Conversion and Management, Volume 259,2022,115571,ISSN 0196-8904.
https://doi.org/10.1016/j.enconman.2022.115571
The integral dissolution heat of the acid-base neutralization was measured in a stirred reactor using a reaction calorimeter (RC1e, Mettler Toledo Ltd.) while LAMBDA DOSER continuously fed acid or base as solids: 23.6 g/min citric acid; 30 g/min NaOH; 21 g/min NaOH; 14.8 g/min NaOH; 7.2 g/min NaOH Ran, Z., Ni, L., Pan, Y., Chen, Y., Wang, J., Jiang, J. & Shu, C-M. (2022). Safety Criteria for Solid–Liquid Heterogeneous Systems in Semibatch Reactors. ACS Omega 2022 7 (24), 21207-21219
https://doi.org/10.1021/acsomega.2c02139
The iron ore charging rate is directly adjusted via the powder-dosing instrument. Zarl, M. A., Ernst, D., Cejka, J., & Schenk, J. (2022). A New Methodological Approach to the Characterization of Optimal Charging Rates at the Hydrogen Plasma Smelting Reduction Process Part 1: Method. Materials, 15(14), 4767.
https://doi.org/10.3390/ma15144767
Dosing of Carajas iron ore. Ernst, D., Zarl, M. A., Cejka, J., & Schenk, J. (2022). A New Methodological Approach on the Characterization of Optimal Charging Rates at the Hydrogen Plasma Smelting Reduction Process Part 2: Results. Materials, 15(12), 4065.
https://doi.org/10.3390/ma15124065
Catalytic pyrolysis experimental setup: A programmable feeder (LAMBDA DOSER 1L) dispensed plastic pellets, typically at a feeding rate of 120 g/h, into aquartz reactor, which contained 1 kg of 8 mm silicon carbide balls. The ball bed was heated and maintained at 500 ◦C for all tests in this study bya programmable microwave heating system. Zhou, N., Dai, L., Lyu, Y., Wang, Y., Li, H., Cobb, K., Chen, P., Lei, H. & Ruan, R. (2022). A structured catalyst of ZSM-5/SiC foam for chemical recycling of waste plastics via catalytic pyrolysis. Chemical Engineering Journal, Volume 440, 2022, 135836, ISSN 1385-8947.
https://doi.org/10.1016/j.cej.2022.135836
2021
Semibatch reaction crystallization study: The solid was dispensed by a LAMBDA DOSER 0.2L and a slow stream of pressurised air was vented through the solid-doser. Three solids were utilized for dosing: CL-20 (150 μm), fine HMX (5 μm) and coarse HMX (300 μm). By mixing the utilised HMX coarse to fine at 5:1, reproducible dispensing was achieved. Herrmannsdörfer, D., & Klapötke, T. M. (2021). Semibatch reaction crystallization for scaled-up production of high-quality CL-20/HMX cocrystal: efficient because of solid dosing. Crystal growth & design, 21(3), 1708-1717.
https://doi.org/10.1021/acs.cgd.0c01611
Solid dosing: A mixture of 90 g CL-20 (205 mmol), 25 g coarse HMX (84 mmol) and 5 g fine HMX (17 mmol) was dispensed by a LAMBDA DOSER 0.2L. A slow stream of pressurised air was vented through the solid doser to prevent cementation of the solid due to acetonitrile vapours. Herrmannsdörfer, D., & Klapötke, T. M. (2021). Quality Assessment of the CL‐20/HMX Cocrystal Utilising Digital Image Processing. Propellants, Explosives, Pyrotechnics, 46(4), 522-529.
https://doi.org/10.1002/prep.202000341
Experimental design for NOx conversion, comprising a vertically-entrained reactor and gas monitoring systems: A calibrated electronic powder doser (Lambda Laboratory Instruments) feeds the recycled plastic (cryogenically pulverised, 150–355 μm) at a constant low feeding rate of 7 mg/min, through a water-cooled probe, into a quartz reactor housed in an electrically heated three-zone furnace. Oluwoye, I., Zeng, Z., Mosallanejad, S., Altarawneh, M., Gore, J., & Dlugogorski, B. Z. (2021). Controlling NOx emission from boilers using waste polyethylene as reburning fuel. Chemical Engineering Journal, 411, 128427.
https://doi.org/10.1016/j.cej.2021.128427
Iron ore and lime feeding system: Continuous loading is carried out using a LAMBDA DOSER 0.2L powder feeding system. The finest ore had strong adhesive properties and strongly caused bridging, which was partially prevented by preheating in a drying oven at 120 °C. Cejka, J. (2021). Parameterevaluierung für den kontinuierlichen Chargiervorgang von Eisenerzen und Zuschlägen im Wasserstoff-Plasma-Schmelzreduktionsprozess. Masterarbeit, Montan Universität Loeben. https://pureadmin.unileoben.ac.at/ws/files/7814331/AC16360490.pdf (2024 April 02)
Determination of the solubility of itaconic acid dosed with a LAMBDA DOSER 0.2L solids feeder controlled by the PLS Holtz, A., Görtz, J., Kocks, C., Junker, M., & Jupke, A. (2021). Automated measurement of pH-dependent solid-liquid equilibria of itaconic acid and protocatechuic acid. Fluid Phase Equilibria, 532, 112893.
https://doi.org/10.1016/j.fluid.2020.112893
2020
Plasma production of nanomaterials: Powdered precursors are introduced with a gravity-fed rotary powder feeder LAMBDA DOSER which is connected to the inlet of the work tube. Graves, B., Engelke, S., Jo, C., Baldovi, H. G., De la Verpilliere, J., De Volder, M., & Boies, A. (2020). Plasma production of nanomaterials for energy storage: continuous gas-phase synthesis of metal oxide CNT materials via a microwave plasma. Nanoscale, 12(8), 5196-5208.
https://doi.org/10.1039/C9NR08886E
https://www.rsc.org/suppdata/c9/nr/c9nr08886e/c9nr08886e1.pdf (2024 April 02)
Scale-up of Dakin–West procedure using glutamic acid at 100 gram scale conducted in an automated setup with a LAMBDA solid DOSER Würdemann, M. A., Niţu, C., De Wildeman, S. M., Bernaerts, K. V., & Orru, R. V. (2020). The Forgotten Pyrazines: Exploring the Dakin–West Reaction. Chemistry–A European Journal, 26(36), 8090-8100.
https://doi.org/10.1002/chem.202000475
Iron ore and lime feeding system: LAMBDA Hi-DOSER 1L powder dosing instrument manufactured by LAMBDA Laboratory Instruments, was used to charge the mixture of iron ore and additives fines continuously into the steel crucible during the test runs. Naseri Seftejani, M. (2020). Reduction of hematite using hydrogen plasma smelting reduction (Doctoral Thesis, Montanuniversitaet Leoben).
https://pure.unileoben.ac.at/en/publications/reduction-of-hematite-using-hydrogen-plasma-smelting-reduction (2024 Feb. 26)
Laboratory Equipment for the hydrogen plasma smelting reduction (HPSR) process: The powder dosing system LAMBDA Hi-DOSER 0.2L was used to introduce continuous ~3 g/min Carajas hematite iron ore with the gas (40 % hydrogen in argon) through the hollow graphite electrode (HGE, inner diameter 5 mm). Zarl, M. A., Farkas, M. A., & Schenk, J. (2020). A study on the stability fields of arc plasma in the HPSR process. Metals, 10(10), 1394.
https://doi.org/10.3390/met10101394
The feeder LAMBDA DOSER was placed on the top of the DTF to continuously and uniformly feed the pulverized coal with a flow rate of 0.6 to 0.7 g/min. Aims to investigate the hydropyrolysis behavior of pulverized bituminous coal in a drop-tube furnace (DTF) with a temperature of 800–1000 °C. Gao, R., Dou, B., Chang, Q., Xu, J., Dai, Z., Yu, G., & Wang, F. (2020). Effect of temperature and hydrogen on product distribution and evolution of char structure during pyrolysis of bituminous coal in a drop tube furnace. Shanghai Engineering Research Center of Coal Gasification, East China University of Science and Technology, Shanghai 200237, PR China.
https://doi.org/10.1016/j.fuel.2020.117078
The solid powder feeding system LAMBDA Hi-DOSER 1L was used to feed the premixed iron ore and lime continuously into the plasma arc zone during the arc operation. The powder dispenser consists of a dosing unit and a powder distributor coupled to a stepping motor to control the number of turns per minute and accordingly the dispensing rate. Seftejani, M. N., Schenk, J., Spreitzer, D., & Zarl, M. A. (2020). Slag Formation during Reduction of Iron Oxide Using Hydrogen Plasma Smelting Reduction. Materials 2020, 13, 935;
https://doi.org/10.3390/ma13040935
2019 Preparation and dosage of alumina feed: To remove any moisture, the alumina was kept in an oven at 300 °C overnight and then stored in a desiccator until electrolysis testing. A LAMBDA DOSER was used for the continuous feed of alumina (feed rates: 200 – 400 mg/min). Medino, C. M. (2019). Improving current efficiency in low-temperature aluminum electrolysis with vertical inert electrodes (Doctoral dissertation).
URI: https://hdl.handle.net/1946/33817 (2024 Mar 27)
Fed-batch enzymatic hydrolysis was conducted in a bioreactor: The pretreated biomass feeding operation was controlled by a programmed LAMBDA DOSER. (Moisture content of substrate: 2.38 %) Tai, C., & Keshwani, D. (2019). System for optimizing fed-batch hydrolysis of biomass. U.S. Patent No. 10,501,766. Washington, DC: U.S. Patent and Trademark Office.
https://patentimages.storage.googleapis.com/a7/d9/fa/6c34de7d414bd1/US10501766.pdf (2024 April 02)
Alumina Feeding: During electrolysis, alumina (aluminum oxide) was continuously fed to the electrolyte with dosing equipment supplied by LAMBDA Laboratory Instruments. The LAMBDA DOSER was adjusted to continuously feed about 70 - 80% of the alumina needed to perform electrolysis at 100 % current efficiency. Gunnarsson, G., Óskarsdóttir, G., Frostason, S., & Magnússon, J. H. (2019). Aluminum electrolysis with multiple vertical non-consumable electrodes in a low temperature electrolyte. In Light Metals 2019 (pp. 803-810). Springer International Publishing.
https://doi.org/10.1007/978-3-030-05864-7_98
Experimental setup: A) gas & solid feeding LAMBDA DOSER systems; B) reaction zone and electrical furnace; C) optical sensing system Díaz, W., Toro, C., Balladares, E., Parra, V., Coelho, P., Reyes, G., & Parra, R. (2019). Spectral characterization of copper and iron sulfide combustion: A multivariate data analysis approach for mineral identification on the blend. Metals, 9(9), 1017.
https://doi.org/10.3390/met9091017
2018
Hybrid solar/autothermal gasifier: The SiC tube was fabricated with a 45˚ 16.7-mm diameter angled hole in the back to allow for a feedstock delivery from a gravity-driven particle feeder LAMBDA DOSER through an Al2O3 tube. The particle feeder was purged with Ar in the feedstock vessel and just below the feeder at a constant rate of 2 LN/min to prevent backflow of reacting gases. The feeder was calibrated with the purge Ar to a feeding rate of ~60 g/h. The feeding rates with 95 % confidence intervals were 57.5 ± 2.7 g/h for activated charcoal and 62.3 ± 8.81 g/h for lignite coal. Muroyama, A. P., Guscetti, I., Schieber, G. L., Haussener, S., & Loutzenhiser, P. G. (2018). Design and demonstration of a prototype 1.5 kWth hybrid solar/autothermal steam gasifier. Fuel, 211, 331-340.
https://doi.org/10.1016/j.fuel.2017.09.059
2016
Feeding operation of fed-batch enzymatic hydrolysis conducted by LAMBDA DOSER which received timely commands from LabVIEW (fuzzy logic control system) Tai, C., Voltan, D. S., Keshwani, D. R., Meyer, G. E., & Kuhar, P. S. (2016). Fuzzy logic feedback control for fed-batch enzymatic hydrolysis of lignocellulosic biomass. Bioprocess and biosystems engineering, 39, 937-944.
https://doi.org/10.1007/s00449-016-1573-1
2015
Pre-treated (oven dried at 60 %, moisture content 2.38 %) lignocellulosic biomass feeding operation for fed-batch enzymatic hydrolysis was controlled by programmed LAMBDA powder DOSER Tai, C., Keshwani, D. R., Voltan, D. S., Kuhar, P. S., & Engel, A. J. (2015). Optimal control strategy for fed‐batch enzymatic hydrolysis of lignocellulosic biomass based on epidemic modeling. Biotechnology and bioengineering, 112(7), 1376-1382.
https://doi.org/10.1002/bit.25552
Pyrolysis and determination of kinetic parameters with LAMBDA DOSER 1L for powder feeding: The fluidization system fed the acid hydrolysis solid residue (AHR) from miscanthus at a substantially constant rate and without blocking. In some experiments, biomass suddenly fell into the reactor due to bridging and electrostatic agglomeration of the starting material. The agglomeration was easily destroyed by tapping on the glass vessel. The motor was set at 005 (near minimum) to achieve flow rates below 1 g/min at a gas flow of 8 L/min. Improvements are being considered to achieve different combinations of feed rate and gas flow with the aim of modifying the solids residence time and equivalence ratio for gasification. Cortes Benitez, A. (2015). Thermal processing of miscanthus, sugarcane bagasse, sugarcane trash and their acid hydrolysis residues (Doctoral dissertation, Aston University).
https://publications.aston.ac.uk/id/eprint/25492/3/Thermal_processing_of_miscanthus_sugarcane_bagasse_sugarcane_trash_and_their_acid_hydrolysis_residues.pdf (2024 April 02)
Applicability study of melted inorganic salts in the pyrolysis process: The LAMBDA DOSER 0.2L dosing device was filled with the feed material, consisting of feedstock (beech wood chips, Virgen-PET or Organosolv lignin) and carbonate salt mixture (carbonate salt mixture of dried Li2CO3 (purum), Na2CO3 (Anhydrous, free -flowing, Redi-Dri™,ACS-reagent), K2CO3 (Anhydrous, free-flowing, Redi-Dri™,ACS-reagent) from Sigma-Aldrich Chemie GmbH) and flushed with nitrogen: 5 g of dried feed material were constantly feeded during 20 minutes into the reactor. Nieberl, M. (2015). Parameterstudie zur thermochemischen Zersetzung organischer Materialien in geschmolzenen Salzen. Bachelor Thesis, Fraunhofer Institut für Chemische Technologie ICT, Pfinztal.
https://doi.org/10.24406/publica-fhg-282280 ,
https://publica-rest.fraunhofer.de/server/api/core/bitstreams/43fc3357-47ba-4bc4-a2d5-b6394d0131c0/content (2024 April 02), see „Abbildung 3-1 Abbildung der Versuchsanlage“
2014
Established amounts of spherical and transparent glass particles simulating fuel droplets were introduced into the channel using LAMBDA powder dosing device Bodoc, V., & Voicu, D. (2014, July). Experimental investigation of the infrared extinction limitations for vapor concentration measurement in a gas/particle flow. In 17th International Symposium on Applications of Laser Techniques to Fluid Mechanics.
HAL Id : hal-01079181 , version 1
https://hal.archives-ouvertes.fr/hal-01079181/document (2024 Feb 22)
Dried and sieved bagasse particles were fed by the calibrated feeder (LAMBDA DOSER) into the drop-tube trickle-bed reactor Krüsi, M. (2014). Heat transfer enhancement in a solar biomass gasifier. Eidgenössische Technische Hochschule ETH Zürich (Nr. 21821).
https://doi.org/10.3929/ethz-a-010256755
2013
The reactor is fitted with the LAMBDA POWDER DOSER to supply solid NaBH4 continuously Muir, Sean S. (2013). Sodium borohydride production and utilisation for improved hydrogen storage. PhD Thesis. Australian Institute for Bioengineering and Nanotechnology, The University of Queensland. https://doi.org/10.14264/uql.2016.540
2012
Copper chloride fed into the quartz reactor by LAMBDA Powder Feeder for producing carbon-coated copper nanoparticles by vapor-phase reduction Eiroma, K., Forsman, J., Hult, E.-L., Auvinen, A., Sipiläinen-Malm, T., Alastalo, A., Tapper, U., Leppäniemi, J., Mattila, P., Lyyränen, J., Sarlin, J., Jokiniemi, J., & Mössmer, S. (2012). Water-Based Carbon-Coated Copper Nanoparticle-Fluid Formation of Conductive Layers at Low Temperature by Spin Coating and Inkjet Deposition. Journal of Imaging Science and Technology, 56(4), 40501-1-40501-10 (10).
https://doi.org/10.2352/J.ImagingSci.Technol.2012.56.4.040501
2011
LAMBDA Powder DOSER used as a particle feeder for Drop Tube Reactor (DTR) Hampp, F., & Janajreh, I. (2011). Development of a drop tube reactor to test and assist a sustainable manufacturing process. In Advances in Sustainable Manufacturing: Proceedings of the 8th Global Conference on Sustainable Manufacturing (pp. 141-148). Springer Berlin Heidelberg.
https://doi.org/10.1007/978-3-642-20183-7_21
Continuous feeding of Copper chloride powder on alumina (Al2O3) pellet bed within a quartz glass nanoparticle reactor to develop Carbon coated copper nanoparticle Inkjet Fluid Eiroma, K., Auvinen, A., Forsman, J., Hult, E. L., Jokiniemi, J., Koskela, P., Sarlin, J., Sipiläinen-Malm, T., & Tapper, U. (2011, January). Development of conductive carbon coated copper nanoparticle inkjet fluid. In NIP & Digital Fabrication Conference (Vol. 2011, No. 2, pp. 458-461). Society for Imaging Science and Technology.
https://citeseerx.ist.psu.edu/doc_view/pid/d22f2a68bdaaa4054fc32e50d30afa87ef2c185c (2024 Feb. 22)
PDF: https://citeseerx.ist.psu.edu/document?repid=rep1&type=pdf&doi=d22f2a68bdaaa4054fc32e50d30afa87ef2c185c (2024 Feb. 22)
2007 Timed particle additions using LAMBDA Powder DOSER to study the fabrication and evaluation of the ferroelectric reinforced metal matrix composites (FR-MMCs) Poquette, B. D. (2007). Understanding Ferroelastic Domain Reorientation as a Damping Mechanism in Ferroelectric Reinforced Metal Matrix Composites (Doctoral dissertation, Virginia Tech).
https://hdl.handle.net/10919/29169 (2024 Feb. 22)
The heat treated wet-silica solid was loaded in the LAMBDA solid DOSER and added to the reactor. Luo, L., Rix, F. C., Stevens, K. A., Kuo, C. L., Zhang, X., Lovell, J. A., Harlan, C.J., Ye, X., & Berg, B. R. (2024). Improved In-Situ MAO Derived Silica Supported Single-Site Metallocene Catalysts. U.S. Patent Application No. 18/253,867.
https://patents.google.com/patent/US20240092947A1/en (2024 June 17)
For “flash pyrolysis” experiments, the powdered biomass (mixture of cellulose, hemicellulose, lignin and ash) was fed into the nitrogen line inside a venturi using a „dust feeder“ LAMBDA Hi-DOSER at a rate between 1 and 20 g/mn. Proust, C., Proust, M., & Foyer, J. (2024, February). High temperature pyrolysis of lignocellulosic biomass for biogas production. In Technological Systems, Sustainability and Safety.
https://hal.science/hal-04538203 (2024 May 14)
Solids segregation studies: The solids dispenser on the top of the fluidized bed reactor was a LAMBDA DOSER 3L that added continuous solid at a speed of up to 13.7 g/min. Ciércoles, R., Lasobras, J., Soler, J., Herguido, J., & Menéndez, M. (2024). A Preliminary Assessment of Sorption Enhanced Methanol Synthesis in a Fluidized Bed Reactor with Selective Addition/Removal of the Sorbent. Removal of the Sorbent.
https://dx.doi.org/10.2139/ssrn.4735903
Before starting pyrolysis, 6 g materials were mixed evenly and added to the feeder LAMBDA DOSER 0.2L Wang, X., Peng, Y., Zhou, R., Fan, L., Zhang, Q., Cui, X., Wu, Q., Zeng, W., Tian, X., Ke, L., Ruan, R., & Wang, Y. (2024). Production of monocyclic aromatic hydrocarbons from microwave co-pyrolysis of polyethylene terephthalate and low-density polyethylene using coconut husk carbon as microwave absorbent. Chemical Engineering Journal, 150732.
https://doi.org/10.1016/j.cej.2024.150732
Study about the significance of feedstock characteristics (moisture, volatile matter, fixed carbon and ash contents) during the particle feeding stage for downdraft gasification of biomass waste: Lambda powder dosing equipment (LAMBDA DOSER 0.2L) was used for particle feeding (date palm waste, olive pomace, sewage sludge) and gasifier flow rate, power rating & storage time were tested. Khan, S., Adeyemi, I., Moustakas, K., & Janajreh, I. (2024). Investigating the characteristics of biomass wastes via particle feeder in downdraft gasifier. Environmental Research, 118597.
https://doi.org/10.1016/j.envres.2024.118597
2023
The automatic dosing equipment LAMBDA DOSER was used to feed continuously 70 % – 80 % of Al2O3 required for theoretical 100 % current efficiency. The system limites due to critical clogging in the alumina feeding channel were reached in some cases after 6 to 10 h. Singh, K., Gunnarsson, G., Magnusson, J. H., Haarberg, G. M., & Saevarsdottir, G. (2023). Performance Evaluation of Low-Temperature KF-NaF-AlF3 Electrolytes for Aluminum Electrolysis Using Vertical Inert Cu–Ni–Fe Alloy Anodes. Journal of The Electrochemical Society, 170(11), 113507.
https://doi.org/10.1149/1945-7111/ad0bae
Lithium-Ion Battery: Feeding of precursor powder (Silicon & ferrocene [Fe(C5H5)2]; 1 g/min) into surface-wave-sustained (SWS) plasma column (core temperature >4000 K) Jie, Z., Zhang, Z., Bai, X., Ma, W., Zhao, X., Chen, Q. & Zhang, G. (2023). Surface-wave-sustained plasma synthesis of graphene@Fe–Si nanoparticles for lithium-ion battery anodes. Appl. Phys. Lett. 11 September 2023; 123 (11): 113902.
https://doi.org/10.1063/5.0159269
2022
The sample of HDPE granules was placed in the glass granule doser (LAMBDA DOSER 1L) Dai, L., Zhou, N., Lv, Y., Cobb, K., Chen, P., Wang, Y., Liu, Y., Zou, R., Lei, H., Mohamed, B. A., Ruan, R., & Cheng, Y. (2022). Catalytic reforming of polyethylene pyrolysis vapors to naphtha range hydrocarbons with low aromatic content over a high silica ZSM-5 zeolite. Science of The Total Environment, 847, 157658.
https://doi.org/10.1016/j.scitotenv.2022.157658
Experimental channel for magnetic particles separation: In the first step, the fly ash was dosed by a LAMBDA dosing system with 1L vessel (mounted above a tray in the middle of the cross-section of the channel) into the horizontal channel and got dispersed by compressed air (3 bar) flowing from a flat nozzle onto the tray. Czech, T. (2022). Morphology and chemical composition of magnetic particles separated from coal fly ash. Materials, 15(2), 528.
https://doi.org/10.3390/ma15020528
Powder dosing of Al2O3 and other dried sieved particles in a closed-loop aerosol generator: The particles were dosed with a volumetric powder doser LAMBDA DOSER 0.2 L into a 1⁄4” T-piece where the powder got picked up by a stream of compressed air (5 L/min) and guided as aerosol through the installation stream. Prüfert, C., Beitz, T., Reich, O. & Löhmannsröben, H.-G. (2022). Inline process analysis of copper-bearing aerosols using laser-induced breakdown spectroscopy, laser-induced incandescence and optical imaging. Spectrochimica Acta Part B: Atomic Spectroscopy 197 (2022) 106527.
https://doi.org/10.1016/j.sab.2022.106527
Coal particles were introduced into the reactor through a N2-purged microprocessor-controlled programmable powder pump feeder (Hi-DOSER, LAMBDA) positioned above the reactor tube...The advantage of this powder pump feeder is that the feeding amount is relatively uniform, avoiding the clogging of the feeder and instability of the gas production. Dai, T., Xu, C., Zhang, Q., Liu, X., Chang, Z. & Yang, Y. (2022). Experimental study of the solar-driven steam gasification of coal in an improved updraft combined drop-tube and fixed-bed reactor. Energy Conversion and Management, Volume 259,2022,115571,ISSN 0196-8904.
https://doi.org/10.1016/j.enconman.2022.115571
The integral dissolution heat of the acid-base neutralization was measured in a stirred reactor using a reaction calorimeter (RC1e, Mettler Toledo Ltd.) while LAMBDA DOSER continuously fed acid or base as solids: 23.6 g/min citric acid; 30 g/min NaOH; 21 g/min NaOH; 14.8 g/min NaOH; 7.2 g/min NaOH Ran, Z., Ni, L., Pan, Y., Chen, Y., Wang, J., Jiang, J. & Shu, C-M. (2022). Safety Criteria for Solid–Liquid Heterogeneous Systems in Semibatch Reactors. ACS Omega 2022 7 (24), 21207-21219
https://doi.org/10.1021/acsomega.2c02139
The iron ore charging rate is directly adjusted via the powder-dosing instrument. Zarl, M. A., Ernst, D., Cejka, J., & Schenk, J. (2022). A New Methodological Approach to the Characterization of Optimal Charging Rates at the Hydrogen Plasma Smelting Reduction Process Part 1: Method. Materials, 15(14), 4767.
https://doi.org/10.3390/ma15144767
Dosing of Carajas iron ore. Ernst, D., Zarl, M. A., Cejka, J., & Schenk, J. (2022). A New Methodological Approach on the Characterization of Optimal Charging Rates at the Hydrogen Plasma Smelting Reduction Process Part 2: Results. Materials, 15(12), 4065.
https://doi.org/10.3390/ma15124065
Catalytic pyrolysis experimental setup: A programmable feeder (LAMBDA DOSER 1L) dispensed plastic pellets, typically at a feeding rate of 120 g/h, into aquartz reactor, which contained 1 kg of 8 mm silicon carbide balls. The ball bed was heated and maintained at 500 ◦C for all tests in this study bya programmable microwave heating system. Zhou, N., Dai, L., Lyu, Y., Wang, Y., Li, H., Cobb, K., Chen, P., Lei, H. & Ruan, R. (2022). A structured catalyst of ZSM-5/SiC foam for chemical recycling of waste plastics via catalytic pyrolysis. Chemical Engineering Journal, Volume 440, 2022, 135836, ISSN 1385-8947.
https://doi.org/10.1016/j.cej.2022.135836
2021
Semibatch reaction crystallization study: The solid was dispensed by a LAMBDA DOSER 0.2L and a slow stream of pressurised air was vented through the solid-doser. Three solids were utilized for dosing: CL-20 (150 μm), fine HMX (5 μm) and coarse HMX (300 μm). By mixing the utilised HMX coarse to fine at 5:1, reproducible dispensing was achieved. Herrmannsdörfer, D., & Klapötke, T. M. (2021). Semibatch reaction crystallization for scaled-up production of high-quality CL-20/HMX cocrystal: efficient because of solid dosing. Crystal growth & design, 21(3), 1708-1717.
https://doi.org/10.1021/acs.cgd.0c01611
Solid dosing: A mixture of 90 g CL-20 (205 mmol), 25 g coarse HMX (84 mmol) and 5 g fine HMX (17 mmol) was dispensed by a LAMBDA DOSER 0.2L. A slow stream of pressurised air was vented through the solid doser to prevent cementation of the solid due to acetonitrile vapours. Herrmannsdörfer, D., & Klapötke, T. M. (2021). Quality Assessment of the CL‐20/HMX Cocrystal Utilising Digital Image Processing. Propellants, Explosives, Pyrotechnics, 46(4), 522-529.
https://doi.org/10.1002/prep.202000341
Experimental design for NOx conversion, comprising a vertically-entrained reactor and gas monitoring systems: A calibrated electronic powder doser (Lambda Laboratory Instruments) feeds the recycled plastic (cryogenically pulverised, 150–355 μm) at a constant low feeding rate of 7 mg/min, through a water-cooled probe, into a quartz reactor housed in an electrically heated three-zone furnace. Oluwoye, I., Zeng, Z., Mosallanejad, S., Altarawneh, M., Gore, J., & Dlugogorski, B. Z. (2021). Controlling NOx emission from boilers using waste polyethylene as reburning fuel. Chemical Engineering Journal, 411, 128427.
https://doi.org/10.1016/j.cej.2021.128427
Iron ore and lime feeding system: Continuous loading is carried out using a LAMBDA DOSER 0.2L powder feeding system. The finest ore had strong adhesive properties and strongly caused bridging, which was partially prevented by preheating in a drying oven at 120 °C. Cejka, J. (2021). Parameterevaluierung für den kontinuierlichen Chargiervorgang von Eisenerzen und Zuschlägen im Wasserstoff-Plasma-Schmelzreduktionsprozess. Masterarbeit, Montan Universität Loeben. https://pureadmin.unileoben.ac.at/ws/files/7814331/AC16360490.pdf (2024 April 02)
Determination of the solubility of itaconic acid dosed with a LAMBDA DOSER 0.2L solids feeder controlled by the PLS Holtz, A., Görtz, J., Kocks, C., Junker, M., & Jupke, A. (2021). Automated measurement of pH-dependent solid-liquid equilibria of itaconic acid and protocatechuic acid. Fluid Phase Equilibria, 532, 112893.
https://doi.org/10.1016/j.fluid.2020.112893
2020
Plasma production of nanomaterials: Powdered precursors are introduced with a gravity-fed rotary powder feeder LAMBDA DOSER which is connected to the inlet of the work tube. Graves, B., Engelke, S., Jo, C., Baldovi, H. G., De la Verpilliere, J., De Volder, M., & Boies, A. (2020). Plasma production of nanomaterials for energy storage: continuous gas-phase synthesis of metal oxide CNT materials via a microwave plasma. Nanoscale, 12(8), 5196-5208.
https://doi.org/10.1039/C9NR08886E
https://www.rsc.org/suppdata/c9/nr/c9nr08886e/c9nr08886e1.pdf (2024 April 02)
Scale-up of Dakin–West procedure using glutamic acid at 100 gram scale conducted in an automated setup with a LAMBDA solid DOSER Würdemann, M. A., Niţu, C., De Wildeman, S. M., Bernaerts, K. V., & Orru, R. V. (2020). The Forgotten Pyrazines: Exploring the Dakin–West Reaction. Chemistry–A European Journal, 26(36), 8090-8100.
https://doi.org/10.1002/chem.202000475
Iron ore and lime feeding system: LAMBDA Hi-DOSER 1L powder dosing instrument manufactured by LAMBDA Laboratory Instruments, was used to charge the mixture of iron ore and additives fines continuously into the steel crucible during the test runs. Naseri Seftejani, M. (2020). Reduction of hematite using hydrogen plasma smelting reduction (Doctoral Thesis, Montanuniversitaet Leoben).
https://pure.unileoben.ac.at/en/publications/reduction-of-hematite-using-hydrogen-plasma-smelting-reduction (2024 Feb. 26)
Laboratory Equipment for the hydrogen plasma smelting reduction (HPSR) process: The powder dosing system LAMBDA Hi-DOSER 0.2L was used to introduce continuous ~3 g/min Carajas hematite iron ore with the gas (40 % hydrogen in argon) through the hollow graphite electrode (HGE, inner diameter 5 mm). Zarl, M. A., Farkas, M. A., & Schenk, J. (2020). A study on the stability fields of arc plasma in the HPSR process. Metals, 10(10), 1394.
https://doi.org/10.3390/met10101394
The feeder LAMBDA DOSER was placed on the top of the DTF to continuously and uniformly feed the pulverized coal with a flow rate of 0.6 to 0.7 g/min. Aims to investigate the hydropyrolysis behavior of pulverized bituminous coal in a drop-tube furnace (DTF) with a temperature of 800–1000 °C. Gao, R., Dou, B., Chang, Q., Xu, J., Dai, Z., Yu, G., & Wang, F. (2020). Effect of temperature and hydrogen on product distribution and evolution of char structure during pyrolysis of bituminous coal in a drop tube furnace. Shanghai Engineering Research Center of Coal Gasification, East China University of Science and Technology, Shanghai 200237, PR China.
https://doi.org/10.1016/j.fuel.2020.117078
The solid powder feeding system LAMBDA Hi-DOSER 1L was used to feed the premixed iron ore and lime continuously into the plasma arc zone during the arc operation. The powder dispenser consists of a dosing unit and a powder distributor coupled to a stepping motor to control the number of turns per minute and accordingly the dispensing rate. Seftejani, M. N., Schenk, J., Spreitzer, D., & Zarl, M. A. (2020). Slag Formation during Reduction of Iron Oxide Using Hydrogen Plasma Smelting Reduction. Materials 2020, 13, 935;
https://doi.org/10.3390/ma13040935
2019 Preparation and dosage of alumina feed: To remove any moisture, the alumina was kept in an oven at 300 °C overnight and then stored in a desiccator until electrolysis testing. A LAMBDA DOSER was used for the continuous feed of alumina (feed rates: 200 – 400 mg/min). Medino, C. M. (2019). Improving current efficiency in low-temperature aluminum electrolysis with vertical inert electrodes (Doctoral dissertation).
URI: https://hdl.handle.net/1946/33817 (2024 Mar 27)
Fed-batch enzymatic hydrolysis was conducted in a bioreactor: The pretreated biomass feeding operation was controlled by a programmed LAMBDA DOSER. (Moisture content of substrate: 2.38 %) Tai, C., & Keshwani, D. (2019). System for optimizing fed-batch hydrolysis of biomass. U.S. Patent No. 10,501,766. Washington, DC: U.S. Patent and Trademark Office.
https://patentimages.storage.googleapis.com/a7/d9/fa/6c34de7d414bd1/US10501766.pdf (2024 April 02)
Alumina Feeding: During electrolysis, alumina (aluminum oxide) was continuously fed to the electrolyte with dosing equipment supplied by LAMBDA Laboratory Instruments. The LAMBDA DOSER was adjusted to continuously feed about 70 - 80% of the alumina needed to perform electrolysis at 100 % current efficiency. Gunnarsson, G., Óskarsdóttir, G., Frostason, S., & Magnússon, J. H. (2019). Aluminum electrolysis with multiple vertical non-consumable electrodes in a low temperature electrolyte. In Light Metals 2019 (pp. 803-810). Springer International Publishing.
https://doi.org/10.1007/978-3-030-05864-7_98
Experimental setup: A) gas & solid feeding LAMBDA DOSER systems; B) reaction zone and electrical furnace; C) optical sensing system Díaz, W., Toro, C., Balladares, E., Parra, V., Coelho, P., Reyes, G., & Parra, R. (2019). Spectral characterization of copper and iron sulfide combustion: A multivariate data analysis approach for mineral identification on the blend. Metals, 9(9), 1017.
https://doi.org/10.3390/met9091017
2018
Hybrid solar/autothermal gasifier: The SiC tube was fabricated with a 45˚ 16.7-mm diameter angled hole in the back to allow for a feedstock delivery from a gravity-driven particle feeder LAMBDA DOSER through an Al2O3 tube. The particle feeder was purged with Ar in the feedstock vessel and just below the feeder at a constant rate of 2 LN/min to prevent backflow of reacting gases. The feeder was calibrated with the purge Ar to a feeding rate of ~60 g/h. The feeding rates with 95 % confidence intervals were 57.5 ± 2.7 g/h for activated charcoal and 62.3 ± 8.81 g/h for lignite coal. Muroyama, A. P., Guscetti, I., Schieber, G. L., Haussener, S., & Loutzenhiser, P. G. (2018). Design and demonstration of a prototype 1.5 kWth hybrid solar/autothermal steam gasifier. Fuel, 211, 331-340.
https://doi.org/10.1016/j.fuel.2017.09.059
2016
Feeding operation of fed-batch enzymatic hydrolysis conducted by LAMBDA DOSER which received timely commands from LabVIEW (fuzzy logic control system) Tai, C., Voltan, D. S., Keshwani, D. R., Meyer, G. E., & Kuhar, P. S. (2016). Fuzzy logic feedback control for fed-batch enzymatic hydrolysis of lignocellulosic biomass. Bioprocess and biosystems engineering, 39, 937-944.
https://doi.org/10.1007/s00449-016-1573-1
2015
Pre-treated (oven dried at 60 %, moisture content 2.38 %) lignocellulosic biomass feeding operation for fed-batch enzymatic hydrolysis was controlled by programmed LAMBDA powder DOSER Tai, C., Keshwani, D. R., Voltan, D. S., Kuhar, P. S., & Engel, A. J. (2015). Optimal control strategy for fed‐batch enzymatic hydrolysis of lignocellulosic biomass based on epidemic modeling. Biotechnology and bioengineering, 112(7), 1376-1382.
https://doi.org/10.1002/bit.25552
Pyrolysis and determination of kinetic parameters with LAMBDA DOSER 1L for powder feeding: The fluidization system fed the acid hydrolysis solid residue (AHR) from miscanthus at a substantially constant rate and without blocking. In some experiments, biomass suddenly fell into the reactor due to bridging and electrostatic agglomeration of the starting material. The agglomeration was easily destroyed by tapping on the glass vessel. The motor was set at 005 (near minimum) to achieve flow rates below 1 g/min at a gas flow of 8 L/min. Improvements are being considered to achieve different combinations of feed rate and gas flow with the aim of modifying the solids residence time and equivalence ratio for gasification. Cortes Benitez, A. (2015). Thermal processing of miscanthus, sugarcane bagasse, sugarcane trash and their acid hydrolysis residues (Doctoral dissertation, Aston University).
https://publications.aston.ac.uk/id/eprint/25492/3/Thermal_processing_of_miscanthus_sugarcane_bagasse_sugarcane_trash_and_their_acid_hydrolysis_residues.pdf (2024 April 02)
Applicability study of melted inorganic salts in the pyrolysis process: The LAMBDA DOSER 0.2L dosing device was filled with the feed material, consisting of feedstock (beech wood chips, Virgen-PET or Organosolv lignin) and carbonate salt mixture (carbonate salt mixture of dried Li2CO3 (purum), Na2CO3 (Anhydrous, free -flowing, Redi-Dri™,ACS-reagent), K2CO3 (Anhydrous, free-flowing, Redi-Dri™,ACS-reagent) from Sigma-Aldrich Chemie GmbH) and flushed with nitrogen: 5 g of dried feed material were constantly feeded during 20 minutes into the reactor. Nieberl, M. (2015). Parameterstudie zur thermochemischen Zersetzung organischer Materialien in geschmolzenen Salzen. Bachelor Thesis, Fraunhofer Institut für Chemische Technologie ICT, Pfinztal.
https://doi.org/10.24406/publica-fhg-282280 ,
https://publica-rest.fraunhofer.de/server/api/core/bitstreams/43fc3357-47ba-4bc4-a2d5-b6394d0131c0/content (2024 April 02), see „Abbildung 3-1 Abbildung der Versuchsanlage“
2014
Established amounts of spherical and transparent glass particles simulating fuel droplets were introduced into the channel using LAMBDA powder dosing device Bodoc, V., & Voicu, D. (2014, July). Experimental investigation of the infrared extinction limitations for vapor concentration measurement in a gas/particle flow. In 17th International Symposium on Applications of Laser Techniques to Fluid Mechanics.
HAL Id : hal-01079181 , version 1
https://hal.archives-ouvertes.fr/hal-01079181/document (2024 Feb 22)
Dried and sieved bagasse particles were fed by the calibrated feeder (LAMBDA DOSER) into the drop-tube trickle-bed reactor Krüsi, M. (2014). Heat transfer enhancement in a solar biomass gasifier. Eidgenössische Technische Hochschule ETH Zürich (Nr. 21821).
https://doi.org/10.3929/ethz-a-010256755
2013
The reactor is fitted with the LAMBDA POWDER DOSER to supply solid NaBH4 continuously Muir, Sean S. (2013). Sodium borohydride production and utilisation for improved hydrogen storage. PhD Thesis. Australian Institute for Bioengineering and Nanotechnology, The University of Queensland. https://doi.org/10.14264/uql.2016.540
2012
Copper chloride fed into the quartz reactor by LAMBDA Powder Feeder for producing carbon-coated copper nanoparticles by vapor-phase reduction Eiroma, K., Forsman, J., Hult, E.-L., Auvinen, A., Sipiläinen-Malm, T., Alastalo, A., Tapper, U., Leppäniemi, J., Mattila, P., Lyyränen, J., Sarlin, J., Jokiniemi, J., & Mössmer, S. (2012). Water-Based Carbon-Coated Copper Nanoparticle-Fluid Formation of Conductive Layers at Low Temperature by Spin Coating and Inkjet Deposition. Journal of Imaging Science and Technology, 56(4), 40501-1-40501-10 (10).
https://doi.org/10.2352/J.ImagingSci.Technol.2012.56.4.040501
2011
LAMBDA Powder DOSER used as a particle feeder for Drop Tube Reactor (DTR) Hampp, F., & Janajreh, I. (2011). Development of a drop tube reactor to test and assist a sustainable manufacturing process. In Advances in Sustainable Manufacturing: Proceedings of the 8th Global Conference on Sustainable Manufacturing (pp. 141-148). Springer Berlin Heidelberg.
https://doi.org/10.1007/978-3-642-20183-7_21
Continuous feeding of Copper chloride powder on alumina (Al2O3) pellet bed within a quartz glass nanoparticle reactor to develop Carbon coated copper nanoparticle Inkjet Fluid Eiroma, K., Auvinen, A., Forsman, J., Hult, E. L., Jokiniemi, J., Koskela, P., Sarlin, J., Sipiläinen-Malm, T., & Tapper, U. (2011, January). Development of conductive carbon coated copper nanoparticle inkjet fluid. In NIP & Digital Fabrication Conference (Vol. 2011, No. 2, pp. 458-461). Society for Imaging Science and Technology.
https://citeseerx.ist.psu.edu/doc_view/pid/d22f2a68bdaaa4054fc32e50d30afa87ef2c185c (2024 Feb. 22)
PDF: https://citeseerx.ist.psu.edu/document?repid=rep1&type=pdf&doi=d22f2a68bdaaa4054fc32e50d30afa87ef2c185c (2024 Feb. 22)
2007 Timed particle additions using LAMBDA Powder DOSER to study the fabrication and evaluation of the ferroelectric reinforced metal matrix composites (FR-MMCs) Poquette, B. D. (2007). Understanding Ferroelastic Domain Reorientation as a Damping Mechanism in Ferroelectric Reinforced Metal Matrix Composites (Doctoral dissertation, Virginia Tech).
https://hdl.handle.net/10919/29169 (2024 Feb. 22)
What is the lead time of Powder Doser?
We have DOSERs in stock and it can be delivered to you within a few days from order. Practically, it is only the time taken for shippingDo you accept Credit Card payments?
You can pay using your credit card via PayPal. Most importantly, it is not necessary to have a PayPal account to make the payment via credit card.Could you please confirm the particle size that can be fed by the dosing system?
The biggest particle size for powders that could be dosed with our DOSER is about 4 mm. A good dosing of powders depends essentially on the flowing properties of the respective powders to be dosed. In general, homogeneous and free-flowing powders can be dosed best.How does the LAMBDA DOSER work with the substances which are prone to agglomeration?
The powder / granules / solid must be properly treated for good flowing properties It is also possible to allow a gas flow to pass through the Lambda dosing vessel in order to create a controlled atmosphere.It is often possible to substantially improve the flowing properties of the respective powder / granules / solid by adding Aerosil (fumed silica – pure SiO2) to your powder (~0.1 - 2% by weight).
How the LAMBDA DOSER reacts to abrasive powders?
In the case of abrasive materials being used with the LAMBDA Powder DOSER, you will have an opportunity to replace the glass vessel and / or the distributors as needed.What is the accuracy of the each dispensing?
The motor of the driving unit is controlled with quartz-driven electronics, similarly as it is done in electronic watches.Therefore, the accuracy depends mainly on the powder. For best accuracy and precise doses, the powder needs to be free-flowing and homogeneous.Can the DOSER control the mass flow rate (g/min) of the powder being dispensed?
It is always possible to control the mass flow rate of the powder using the LAMBDA Doser. You could program the DOSER up to 27 pairs of speed and time settings to control your desired mass flow rate (g/min).Is it possible to control the DOSER via Mettler Toledo titroprocessor to dispense NaF to the titration process when required?
Yes, the powder DOSER can be controlled by Mettler Titration Excellence T50/T70/T90 via RS-232 communication (most common type of connection with Mettler accessories), to dispense the desired amount of powder to the titration process.The powder DOSER has to be included as RS-232 control in the titroprocessor unit and the desired activity can be selected (e.g.: the signal would switch off the DOSER or switch it on, etc.)
For integration of DOSER with your Mettler titroprocessor, you would need the RS-232 interface activated in the powder dosing unit and RS-232 connection cable.